Scott + Partners Earns Two Awards at Efficiency Vermont’s Best of the Best 2017
The Darling Inn Apartments project took an existing historic building in Lyndonville, Vermont and renovated it, giving it an energy-efficient makeover. We paid special attention to sealing and insulating the building shell, while maintaining the historic look and feel. Existing insulation in the attic, slopes and knee walls was removed and replaced with significantly tighter insulation and air seals. The existing heating system (an oil boiler with electric resistance storage heaters) was removed and replaced with a new wood pellet boiler with hydronic distribution and indirect DHW. Additionally, a whole building energy recovery ventilation system was installed. This allows proper ventilation of the entire building without adding significantly to the heating load, since exhaust air is recovered and used to preheat incoming fresh air. The energy savings with this system is notable.
PROJECTED ANNUAL Btu SAVINGS:
631.7 mmBtu
PROJECTED ANNUAL $$ SAVINGS:
$24,464 (space heat and DHW)
PROJECTED ANNUAL $$ SAVINGS:
$2,404 (lighting upgrades)
PORTION OF SAVINGS FROM ERV:
210.9 mmBtu
$3,466 annual
– – –
Downstreet Housing and Community Development provides high-quality, safe, affordable housing to the residents of Barre and the central Vermont area. Their goal for this project was to replace three existing poorly functioning and unsafe apartment buildings with a new energy efficient building. They were also looking to replace their existing multilevel, inefficient office space. The final design is a mixed-use building that provides 1- and 2-bedroom units, ample exterior green space, and a new open office suite. Keeping the apartments in the downtown area buttresses Downstreet’s mission, providing residents easy access to shopping, services, and public transportation.
Key Energy Efficiency Measures:
ENVELOPE: We focused on reducing energy consumption through tight air sealing details and insulating the building shell. The project goal for air sealing was 2 ACH50 or less, and the final blower door test result was 0.63 ACH50. Walls are insulated with stone wool insulation between the studs and a continuous two inch layer of stone wool rigid board insulation outside of the exterior sheathing. Siding is a mix of fiber cement product installed on furring strips, creating a rain screen system.
LIGHTING: LED lighting was installed throughout the project, for both exterior and interior uses. Occupancy sensors were installed in offices and corridors throughout the building. Interior configuration is designed to get a good quality of daylight throughout. We are saving 7,789kWh from interior and exterior lighting and controls. Interior LPD savings is 14% better than code, and exterior is 69% better than code.
HVAC: This project utilizes a high efficiency, wood pellet boiler system. Wood pellet fuel burns clean, supports the regional economy, and lowers heating costs compared to traditional heating oil and propane systems. Fresh air is distributed throughout the building from roof-mounted ERV units. Windows in the apartments and offices are operable. All finishes installed in the building were required to meet the Greenguard, Green Seal or an equivalent standard.
OTHER EQUIPMENT: Framing materials and wood siding for this project were specified to be from within a 300-mile radius of the project site. Kitchen cabinets and bathroom vanities were specified to be fabricated from FSC-certified materials. Durable finish choices were specified to utilize renewable and rapidly-renewable materials such as Linoleum flooring. Low- and no-VOC paints, primers, adhesives, and sealants were used to help maximize indoor air quality. Materials were locally and regionally sourced when possible. All appliances in the project are new and Energy Star rated. Common laundry areas use energy and water efficient models. The building roof is designed to be PV ready.
WATER: Storm-water is collected from low-pitched roofs and managed with a roof drain collection system tied to the city storm system. On-site storm-water collection is managed by the new green scape. All bathrooms and kitchens throughout the project are equipped with new efficient fixtures, including low flow toilets, shower heads (1.5 GPM), and aerators at faucets (1.5 GPM kitchen & 1.0 GPM bathroom).
ENERGY MANAGEMENT PRACTICES: An operations & management manual was created to educate the building occupants on how to maintain efficiences. Building management staff were trained by the equipment installers on proper operation + management of the mechanical systems.
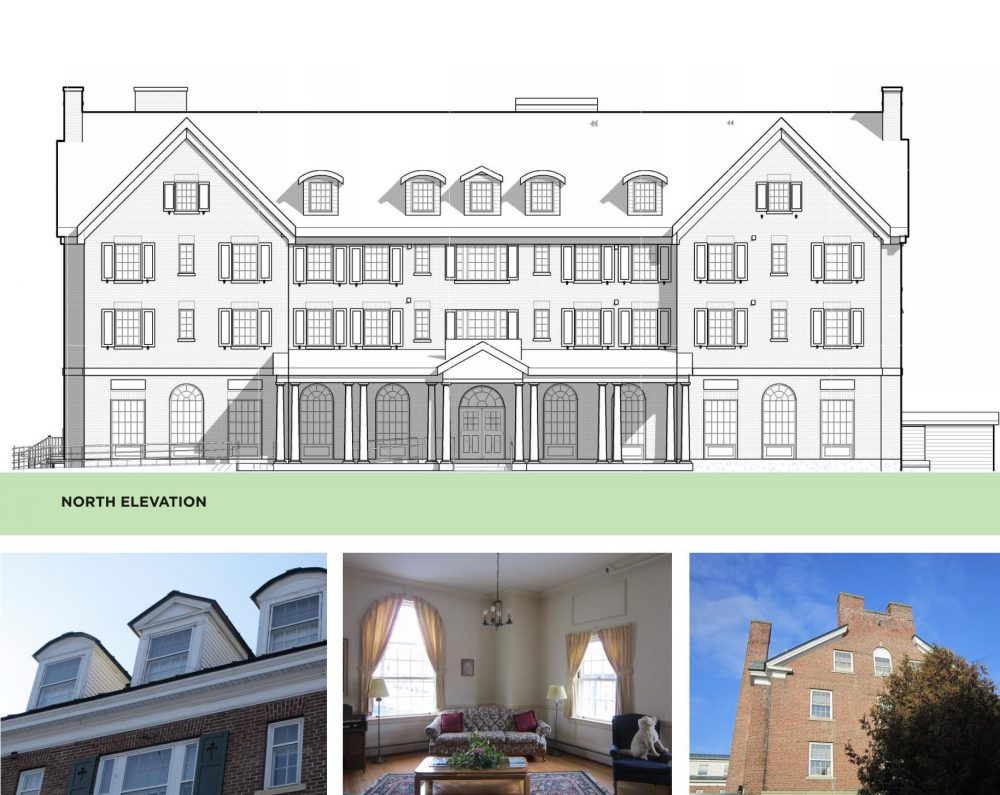